A talc grinding plant is a facility designed to crush, grind, and process talc into a fine powder that can be used for a variety of industrial applications.
Talc, also known as hydrated magnesium silicate, is a soft mineral that is commonly used as a filler in a wide range of products, including cosmetics, ceramics, paper, and plastics.
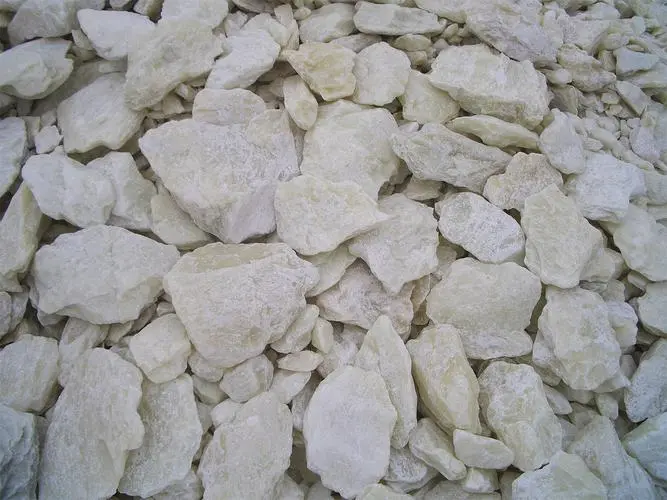
Talc
The process of talc grinding typically involves crushing the raw talc materials, and then using various types of grinding equipment, such as ball mills, jet mills, and roller mills, to reduce the particle size of the talc to a fine powder. The ground talc powder is then further processed and refined to remove impurities and improve its properties, such as whiteness, brightness, and fineness.
Talc grinding plants may vary in size and complexity depending on the desired output and the specific requirements of the end-use applications. Some talc grinding plants may be large, automated facilities, while others may be small, manual operations. The process of talc grinding can also be customized to meet specific requirements, such as particle size distribution, purity, and color.
Overall, talc grinding plants play an important role in the production of a wide range of products and are an essential component of many industrial processes.
Advantages and disadvantages of various talc grinding mills
There are several types of mills that can be used for grinding talc into a fine powder, each with their own advantages and disadvantages. Here are some of the most common types of mills used for talc grinding:
- Ball mills: Ball mills are commonly used for talc grinding because they are simple to operate and have a low energy consumption. They are also versatile and can be used for wet or dry grinding. However, ball mills have a low grinding efficiency and may require long grinding times to produce a fine powder.
- Jet mills: Jet mills use high-speed air jets to grind talc into a fine powder. They are highly efficient and can produce a narrow particle size distribution. However, jet mills are expensive to operate and require specialized equipment for their operation.
- Roller mills: Roller mills use a series of rollers to crush and grind talc into a fine powder. They are efficient and have a high grinding capacity. However, roller mills may produce a coarser powder than other types of mills.
- Raymond mills: Raymond mills are commonly used for talc grinding because they are versatile and have a high grinding efficiency. They can also produce a narrow particle size distribution. However, Raymond mills require frequent maintenance and may have a high operating cost.
- Hammer mills: Hammer mills are sometimes used for talc grinding, especially for coarse grinding. They are simple to operate and have a low operating cost. However, they may produce a large amount of dust during operation.
In summary, the advantages and disadvantages of each type of talc grinding mill depend on the specific needs of the application. Factors such as particle size distribution, energy efficiency, and operating cost should be considered when selecting a mill for talc grinding.
What factors need to be considered when investing in a talc grinding plant?
Investing in a talc grinding plant requires careful consideration of several factors to ensure that the investment is successful and profitable. Some of the key factors that need to be considered when investing in a talc grinding plant include:
- Market demand: The demand for talc products and the specific applications where the talc will be used should be evaluated. It's important to assess the current market demand and to anticipate any potential changes in the future.
- Quality of raw materials: The quality and consistency of the raw materials used to produce the talc powder can impact the quality of the final product. It's essential to ensure that the talc source is reliable and consistent.
- Production capacity: The production capacity of the grinding plant should be determined based on the expected demand for the final product. It's important to ensure that the production capacity of the plant is adequate to meet the demand.
- Grinding technology: The choice of grinding technology and equipment used in the talc grinding process can impact the quality and efficiency of the final product. It's essential to select the appropriate grinding technology and equipment that can produce the desired particle size distribution and product quality.
- Operating costs: The operating costs associated with the plant, such as energy consumption, labor costs, maintenance costs, and raw material costs, should be carefully evaluated to ensure that the plant can operate profitably.
- Environmental and regulatory compliance: The environmental and regulatory compliance requirements associated with the operation of a talc grinding plant should be evaluated to ensure that the plant can operate in compliance with local and national regulations.
Overall, investing in a talc grinding plant requires a comprehensive evaluation of various factors to ensure that the investment is profitable and sustainable in the long term.
How much does it cost to invest in a talc grinding plant?
The cost of investing in a talc grinding plant can vary depending on various factors such as the size of the plant, equipment and machinery required, the location of the plant, labor costs, and other related expenses. Additionally, there may be costs associated with obtaining permits, licenses, and complying with regulations.
It is difficult to provide a specific estimate for the cost of investing in a talc grinding plant without knowing the specific details of the project. However, some general estimates suggest that the cost can range from several hundred thousand dollars to several million dollars, depending on the size and complexity of the project.
It is important to conduct a thorough feasibility study and cost analysis before investing in a talc grinding plant to ensure that the project is financially viable and sustainable. Seeking the advice of industry experts and consulting with experienced professionals can also help provide a better estimate of the cost of investing in a talc grinding plant.