CLUM Ultra Fine Powder Grinder Plant can be widely used in chemical, metallurgy, non-metallic mining and other industries, especially in the field of ultra-fine grinding of white non-metallic minerals.
It has excellent performance and can be used for papermaking, coatings, plastics, Rubber, PVC, printing ink and other industries provide high-quality fillers and additives.
It can be widely used in large-scale ultra-fine dry powder processing of non-metallic minerals such as calcite, marble, limestone, dolomite, barite, talc, kaolin, dolomite, wollastonite, gypsum, feldspar, pyrophyllite, etc.
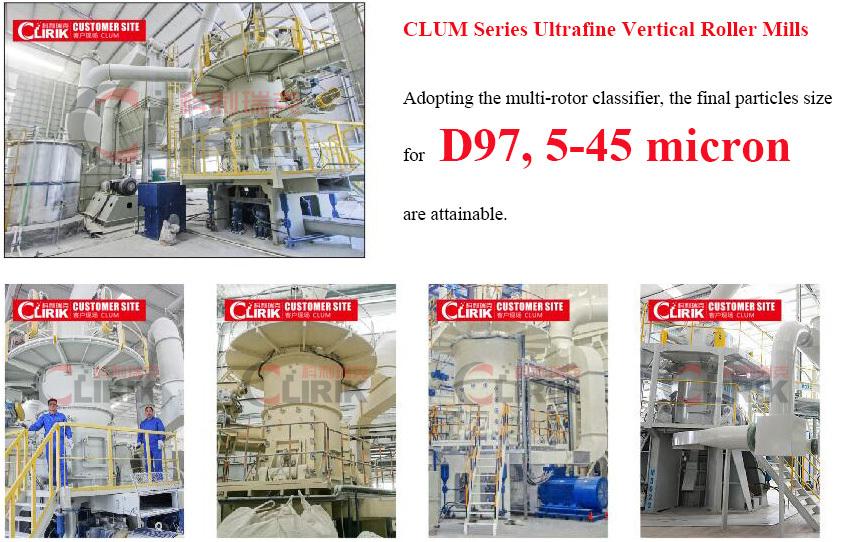
It has excellent performance and can be used for papermaking, coatings, plastics, Rubber, PVC, printing ink and other industries provide high-quality fillers and additives.
It can be widely used in large-scale ultra-fine dry powder processing of non-metallic minerals such as calcite, marble, limestone, dolomite, barite, talc, kaolin, dolomite, wollastonite, gypsum, feldspar, pyrophyllite, etc.
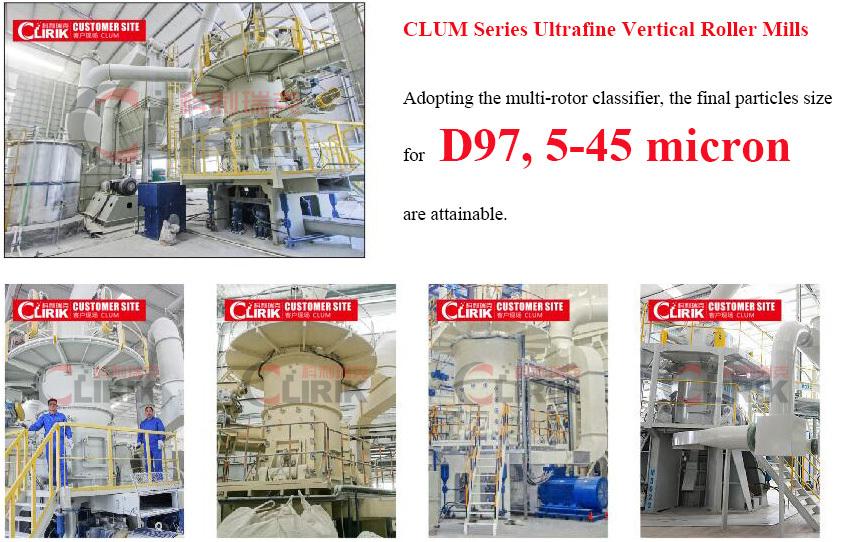
Application range: calcium carbonate processing plant, cement ultrafine powder processing plant, calcite processing plant, barite grinding plant, limestone grinding plant...
Materials: calcite, marble, limestone, talc, barite, brucite, quicklime, gypsum, slag, phosphate and other non-metallic minerals
Features of CLUM Ultra Fine Powder Grinder Plant
Shanghai CLIRIK Machinery Co., Ltd. has combined years of mill production experience to design and develop a model A new type of ultra-fine grinding equipment that integrates grinding, grading, conveying, secondary powder selection, and finished product packaging—CLUM Ultra Fine Powder Grinder Plant.
The product fineness can reach 400-3000 meshes, breaking through the ultra-fine powder The bottleneck of low processing capacity, after 5 years of hard work, CLIRIK Machinery's ultra-fine vertical mill has built 30 ultra-fine powder production lines around the world.
CLUM Ultra Fine Powder Grinder Plant Advantages
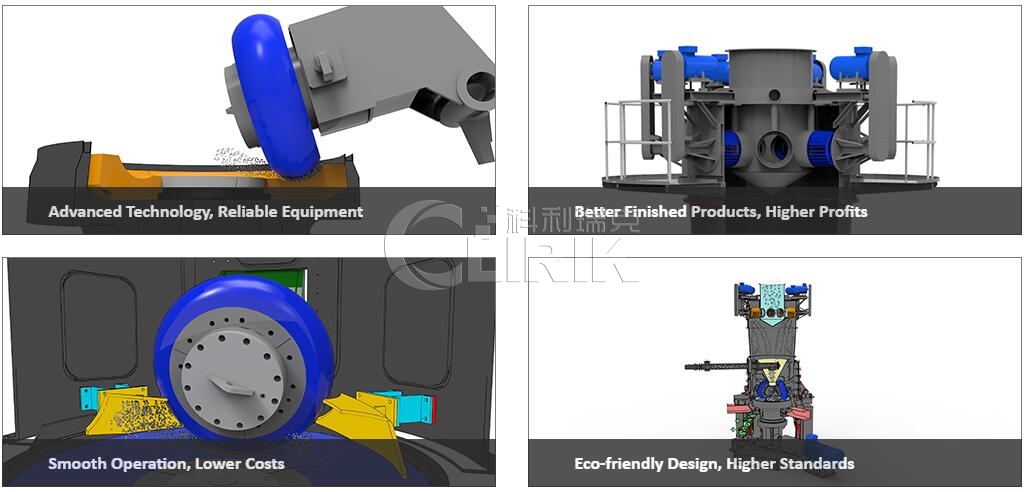
Energy efficient
In the case of the same fineness of the finished product and the same motor power, the output is more than twice that of jet mill, stirring mill, and ball mill.
Long service life of wearing parts
The grinding roller and grinding ring are forged with special materials, which greatly improves the utilization. Generally it can reach more than one year, and the service life can reach 2-5 years when processing calcium carbonate and calcite.
High safety and reliability
Because there is no rolling bearing and no screws in the grinding cavity, there is no problem that the bearings and their seals are easily damaged, and there is no problem that the screws are easy to loosen and damage the machine.
Environmental protection and clean
The pulse dust collector is used to capture dust, and the muffler is used to reduce noise, which is environmentally friendly and clean.
Structure and Composition of CLUM Ultra Fine Powder Grinder Plant
CLUM series ultra-fine powder grinder are mainly composed of electric motors, reducers, grinding wheel devices, grinding disc devices, pressurizing devices, powder separators, feeding devices, oil stations, main engines, and electronic control systems.
- 1. Grinding wheel device: the main part of the material to be rolled, without power output, and passively running due to the friction force in contact with the material.
- 2. Grinding disc device: The grinding area of the material is connected to the reducer and rotates by itself.
- 3. Pressure device: control the gap between the grinding wheel and the grinding disc to ensure the pressure of the grinding wheel during the grinding process.
- 4. Powder separator: The multi-head powder separator structure uses the principle of rotating centrifugal force to achieve fine powder screening and filtration in continuous production. It is an efficient and energy-saving powder separator.
Working Principle of CLUM Ultra Fine Powder Grinder Plant
The main machine motor drives the milling disc to rotate through the reducer. At the same time, the airflow produced by the high-pressure fan enters the main machine from the tuyere. The materials are fed into the main machine of the vertical mill through the feeding screw and fall into the center of the milling disc. Open, when passing through the roller table area on the grinding disc, the large pieces of materials are directly crushed by the pressure of the rollers, and the small particles are pressed and then granulated to further pulverize until they become powder. The powdered material continues to move to the edge of the grinding disc until it is taken away by the strong airflow from the air inlet. When the material in the airflow passes through the upper separator, under the action of the centrifugal force generated by the high-speed rotating impeller, the coarse particles fall into the grinding disc again. After grinding, the qualified powder passes through the powder selection system with the airflow and is collected by the dust collector, which is the finished product.
CLUM Ultra Fine Powder Grinder Plant Parameter
Main configuration and production | |||
---|---|---|---|
Item Model | CLUM1425 | CLUM1632 | CLUM1736 |
Working Diameters(mm) | 1400 | 1600 | 1700 |
Number of rollers(pieces) | 3 | 3 | 3 |
Number of classifier(pieces) | 5 | 7 | 7 |
Power of classifier(Kw) | 5X15 | 7X15 | 7X(15~18.5) |
Main unit power (Kw) | 250 | 315 | 355 |
Blower power(Kw) | 200 | 250 | 315 |
Feed size (mm) | <10mm | <10mm | <10mm |
Moisture of feeding material | <3% | <3% | <3% |
Less than 2μm=34% output(t/h) |
11-14 | 13-17 | 15-19 |
Less than 2μm=46% output(t/h) |
7-8 | 9-10 | 11-12 |
Less than 2μm=60% output(t/h) |
3-4 | / | / |
Material: based on calcite Particle size distribution: measured by micro laser diffraction particle size analyzer in British Malvern3000 instruments |
CLUM1425 Ultrafine Stone Powder Making Machine Technical Parameter
(t/h)Output Item |
11.0-14.0 | 8.0-10.0 | 7.0-8.0 | 5.0-6.0 | 3.0-4.0 |
---|---|---|---|---|---|
specific surface area(cm²/g) | 11000±500 | 13500±500 | 15000±500 | 17000±500 | 19000±500 |
325mesh remaining amount (%) | 0.015 | 0.015 | 0.01 | 0 | 0 |
less than 2μm powder content (%) | 34 | 38 | 46 | 53 | 60 |
Median particle diameter D50 (um) | 4.2 | 3.0 | 2.4 | 1.8 | 1.4 |
General name(mesh) | 600 | 800 | 1250 | 2000 | 2500 |
Particle size distribution D97 (um) | 30 | 25 | 20 | 15 | 9 |
Particle size cut point D100 (um) | 80 | 48 | 38 | 28 | 18 |
Moisture content (%) | <0.3% | <0.3% | <0.3% | <0.3% | <0.3% |
Energy consumption (KW/T) | 38-40 | 40-50 | 47-53 | 50-53 | 110-125 |
CLUM1632 Ultrafine Stone Powder Machine Machine Technical Parameter
(t/h)Output Item |
13.0-17.0 | 11-13 | 9.0-10.0 | 7.0-8.0 |
---|---|---|---|---|
specific surface area(cm²/g) | 11000±500 | 13500±500 | 15000±500 | 17000±500 |
325mesh remaining amount (%) | 0.015 | 0.015 | 0.01 | 0 |
less than 2μm powder content (%) | 34 | 38 | 46 | 53 |
Median particle diameter D50 (um) | 4.2 | 3.0 | 2.4 | 1.8 |
General name(mesh) | 600 | 800 | 1250 | 2000 |
Particle size distribution D97 (um) | 30 | 25 | 20 | 15 |
Particle size cut point D100 (um) | 80 | 48 | 38 | 28 |
Moisture content (%) | <0.3% | <0.3% | <0.3% | <0.3% |
Energy consumption (KW/T) | 38-40 | 40-50 | 47-53 | 50-53 |
CLUM1736 Ultrafine Stone Powder Making Machine Technical Parameter
(t/h)Output Item |
11.0-14.0 | 12.5-14.5 | 10.0-11.0 |
---|---|---|---|
specific surface area(cm²/g) | 11000±500 | 13500±500 | 15000±500 |
325mesh remaining amount (%) | 0.015 | 0.015 | 0.01 |
less than 2μm powder content (%) | 34 | 38 | 46 |
Median particle diameter D50 (um) | 4.2 | 3.0 | 2.4 |
General name(mesh) | 600 | 800 | 1250 |
Particle size distribution D97 (um) | 30 | 25 | 20 |
Particle size cut point D100 (um) | 80 | 48 | 38 |
Moisture content (%) | <0.3% | <0.3% | <0.3% |
Energy consumption (KW/T) | 38-40 | 40-50 | 47-53 |