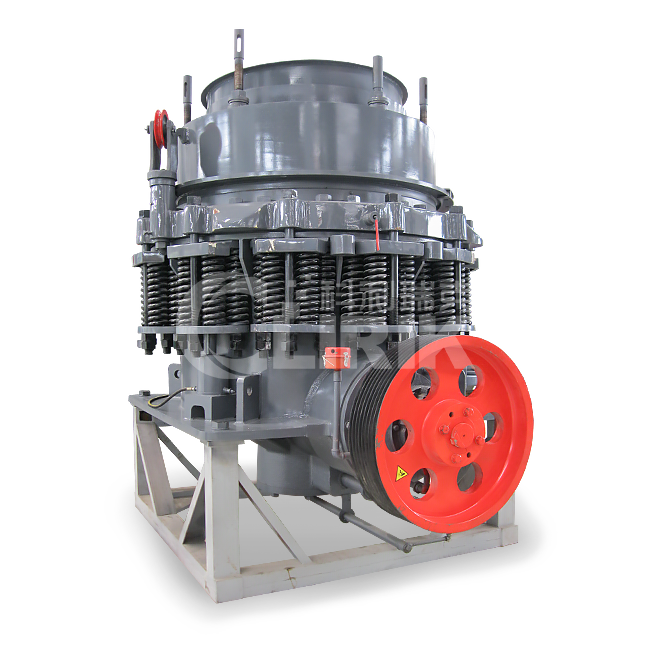
Hydraulic cone crusher is mainly used for the second-stage crushing and third-stage crushing in metal mines and construction sand and gravel processing.
Because the hydraulic cone crusher has a strong crushing capacity and large output. It is more often used in crushing production lines for medium hardness materials such as river pebbles.
Application range: river pebble, granite, basalt, iron ore, limestone, quartzite, diabase, etc.
Materials: sand and gravel yard, mining, coal mining, concrete mixing station, dry mortar, power plant desulfurization, quartz sand, etc.
Feed particle size: 76-290 mm
Production capacity: 120-430 t/h
Features of hydraulic cone crusher
Hydraulic cone crusher is mainly used for the second-stage crushing and third-stage crushing in metal mines and construction sand and gravel processing.
Because of its strong crushing capacity and large output, the sand and gravel production lines using hydraulic cone crushers are more used in rivers.
Crushing of medium and hard materials such as pebbles. In addition, the hydraulic cone crusher has a large iron passing size, and the processed sand and gravel have a high content of granular products below 8mm, which has a great comparative advantage in actual use.
The production requirements of machine-made sand and gravel for construction enjoy high praise among customers.
Performance advantage of hydraulic cone crusher
- 1. High efficiency. Adopting the optimized structure of fixed main shaft and small spherical shaft, which is 5%-15% higher than the efficiency of the old spring cone crusher.
- 2. High output. The perfect combination of crushing stroke, crushing speed and crushing cavity shape is designed, which is higher than the old-fashioned spring cone crusher with higher output and higher quality. Fewer stones and more uniform grain size.
- 3. High stability. When there are hard objects such as iron blocks that cannot be broken into the machine, the over-iron protection device will automatically release them, and then reset immediately.
Structure of hydraulic cone crusher
Hydraulic cone crusher is mainly composed of the base assembly, drive shaft assembly, motor assembly, moving cone assembly, and fixed cone assembly. The auxiliary part consists of the electrical system, lubrication system, hydraulic system, and so on.
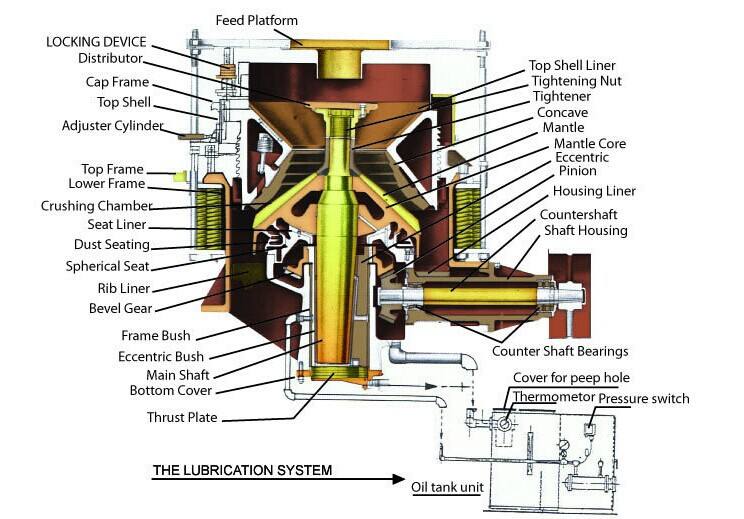
Application of hydraulic cone crusher
- 1. The new hydraulic cone crusher is safer and more stable in operation, convenient in maintenance, short in downtime and guaranteed in output, and is more suitable for large-scale sand and gravel production systems.
- 2. The cone crusher adopts a multi-point split hydraulic lubrication control system, which has stronger bearing lubrication and overload protection capabilities, which greatly improves the automation of the entire production line.
- 3. The cone crusher has re-experimentally designed the cavity type and stroke, which is more suitable for crushing hard materials such as river pebbles, basalt, iron ore, etc. The output is 35%-60% higher than that of ordinary spring cone crushers.
Hydraulic Cone Crusher Second-stage Crushing Cone Crusher Cone Crusher
Working principle
The hydraulic cone crusher makes a swinging motion under the driving action of the eccentric sleeve, which drives the crushing wall to squeeze and grind the material between it and the rolling mortar wall.
According to the lamination theory, the material is subjected to forces in multiple directions, according to its own The texture is broken and polished, and finally, stable stone particles are formed.
Those that meet the discharge requirements fall from the swing gap of the crushing wall, and the remaining materials continue to be broken until the final requirements are met.
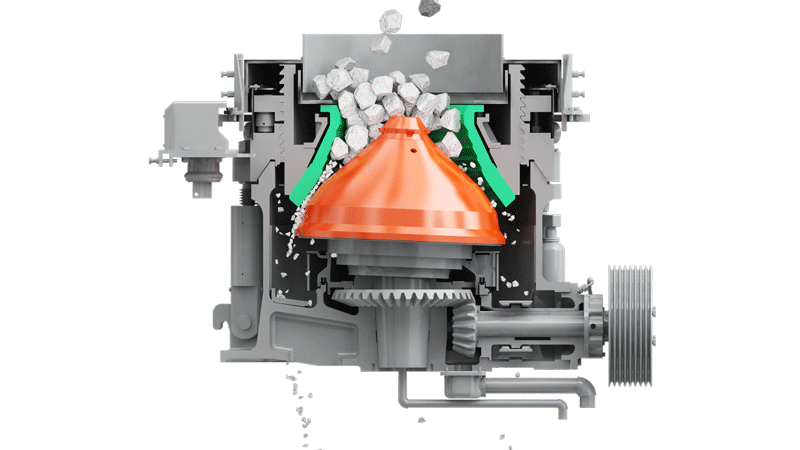
Technical parameter
Model | Cavity | Output port size (mm) | Feeding port size (mm) | Production capacity (t/h) | Diameter of moving cone (mm) | Motor power (kw) | Host weight |
---|---|---|---|---|---|---|---|
HPC-160 | C | 13 | 150 | 120-240 | 950 | 160 | 13 |
F | 6 | 76 | 55-180 | ||||
HPC-220 | C | 13 | 225 | 150-430 | 1160 | 220 | 19 |
F | 6 | 86 | 90-260 | ||||
HPC-315 | C | 13 | 290 | 190-610 | 1400 | 315 | 26 |
F | 6 | 100 | 108-320 | ||||
HPC-400 | C | 13 | 320 | 230-700 | 1500 | 400 | 33 |
F | 6 | 110 | 145-430 |
Questions about cone crusher
Spring Cone Crusher
The motor of the spring cone crusher drives the large bevel gear at the bottom of the eccentric sleeve through the hydraulic coupling and the small bevel gear, so that the eccentric sleeve rotates, causing the cone to swing and crush the material.
The main shaft of the crusher is not moving, but only supports the spherical tile to bear the crushing force.
Because the main shaft of the crusher does not move and the eccentric sleeve transmits the crushing force, the structure can withstand a large crushing force, and is very suitable for fine crushing and ultra-fine crushing, because the crushing force of ultra-fine crushing is very large. It is expected that the product particle size (for ultrafine crushed liner) can reach 50-80% (depending on the nature of the material) when the open circuit is 5mm.
Spring cone crusher is suitable for the third stage crushing or the fourth stage crushing in metal mine concentrators; it is suitable for building materials or non-metallic mines and civil engineering. Especially in areas where the supply of natural sand required for civil engineering is insufficient.
Hydraulic Cone Crusher
The hydraulic cone crusher works by driving the pulley or the coupling, the transmission shaft and the cone part to make the eccentric shaft do periodic swing motion under the axis line through the rotation of the motor.
After the material enters the crushing cavity from the material port, it is crushed by the mutual impact extrusion, grinding and rubbing of the eccentric shaft and the rolling mortar wall.
The hydraulic insurance system can remove the faults from the top of the support sleeve and the fixed cone through the machine when the machine has an iron failure or a stuffy car. It plays a good insurance role and greatly reduces the maintenance rate and improves production. effectiveness.
Cone crusher is secondary crushing equipment often used in mine crushing. The following will briefly introduce you to how to adjust the discharge opening gap of cone crusher:
1. To adjust the discharge, it should be carried out when the main engine is stopped, first select the manual for the safety cylinder and then start the hydraulic oil pump;
2. Start to lock the lock cylinder to retract, wait for the normal pressure indicator to light up, then start to extend and retract;
3. After the material port is adjusted, start the locking cylinder to extend, and stop the hydraulic oil pump when the pressure of the locking cylinder is 0Mpa;
4. The adjustment range of the discharge port is adjusted according to the parameter range specified on the equipment nameplate;
5. Select Auto on the safety cylinder button.
Additional matters:
When the cone crusher is replaced with a new liner, the discharge port of the cone crusher can reach the set value of about 13mm; due to the wear of the crusher, after the liner is worn to a certain extent, the size of the discharge port will expand to about 18mm, which can no longer be used. Adjust downward; when the lining plate is worn to the later stage, the discharge opening will reach about 20mm, which basically cannot achieve the crushing effect.
In order to avoid this situation, the eccentric distance can be adjusted from the original 50mm to 40mm, so that although the material throughput is reduced, the ore discharge opening can be basically maintained at about 13mm, which is beneficial to increase the qualified grain size in the discharge and reduce the return of the ore. .
How to adjust the gap of the cone crusher outlet?
所需时间: 1 小时
How to adjust the gap of the cone crusher outlet?
- 1. To adjust the discharge
To adjust the discharge, it should be carried out when the main engine is stopped, first select the manual for the safety cylinder and then start the hydraulic oil pump;
- 2. Start to lock the lock cylinder to retract
Start to lock the lock cylinder to retract, wait for the normal pressure indicator to light up, then start to extend and retract;
- 3. Stop the hydraulic oil pump
After the material port is adjusted, start the locking cylinder to extend, and stop the hydraulic oil pump when the pressure of the locking cylinder is 0Mpa;
- 4. Adjustment range of the discharge port
The adjustment range of the discharge port is adjusted according to the parameter range specified on the equipment nameplate;
- 5. Select Auto on the safety cylinder button.
Select Auto on the safety cylinder button.
Related Products
Coarse, Fine, Ultrafine Powder Grinding Mills
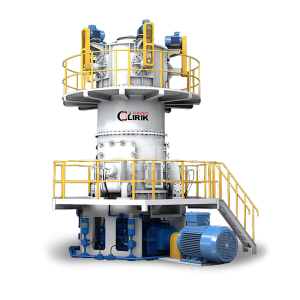
CLUM Ultrafine Powder Vertical Roller Mill
CLUM ultra-fine powder vertical roller mill is mainly suitable for the deep processing of ultra-fine and large-scale powder of non-metallic minerals such as calcite, marble, limestone, talc, barite, brucite, quicklime, gypsum, slag, phosphate, etc.
Capacity: 0.5-45t/h
Finished fineness: 200-3000 mesh
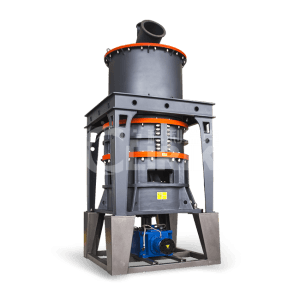
HGM Ultrafine Powder Grinding Mill
HGM Ultrafine Powder Grinding Mill also called ultrafine pulverizer, micro powder grinding mill, limestone grinding mill, calcium carbonate grinding mill. HGM ultrafine powder grinding mill is mainly suitable for superfine powder processing.
Capacity: 0.5-45t/h
Finished fineness: 100-3000 mesh
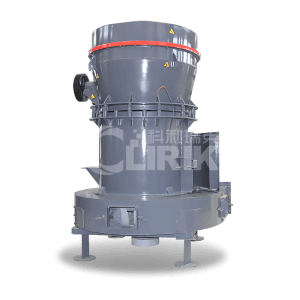
YGM Raymond Roller Grinding Mill
YGM Raymond roller grinding mill is mainly suitable for grinding and processing metallurgy, building materials, chemical industry, mining, and other mineral products.
Capacity: 1.5-40t/h
Finished fineness: 80-600 mesh