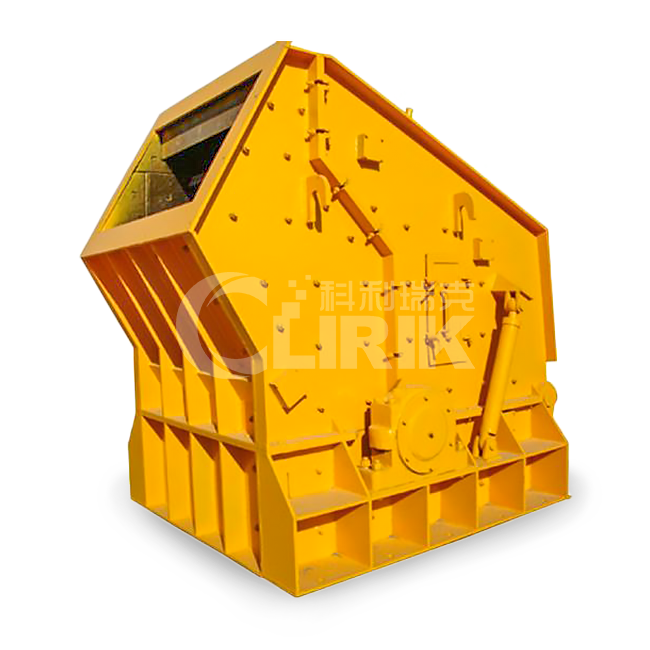
Impact crusher is mainly used in metallurgy, mining, cement, chemical industry, refractory materials and ceramics, and other industrial sectors.
Application range: sand and gravel yard, mining, coal mining, concrete mixing station, dry mortar, power plant desulfurization, quartz sand, etc.
Materials: River pebble, granite, basalt, iron ore, limestone, quartzite, diabase, etc.
Motor power: 30-400 kw
Production capacity: 10-550 t/h
Features of impact crusher
The impact crusher is mainly used in metallurgy, mining, cement, chemical industry, refractory materials and ceramics, and other industrial sectors. The medium-hard ore is subjected to coarse crushing, medium crushing, and fine crushing.
The impact crusher is a new generation of products with an international advanced level of quality, which is absorbed by the new technology of the current international impact crusher.
Impact crushing machine Impact crusher machine Impact stone crusher
In recent years, our factory has specially developed an impact crusher to meet the needs of metallurgy, mining, construction, and other industrial sectors to crush high-strength, high-hardness micro-carbon ferrochromium.
The impact crusher is mainly used for medium-sized crushing of various ores and bulk materials and is widely used in mining, smelting, building materials, highways, railways, water conservancy, and chemical industries.
The high compressive strength of the crushed material is 320MPa.
The impact crusher has a large crushing ratio, uniform product particle size, simple structure, reliable operation, easy maintenance, and low operating costs.
Performance characteristics of impact crusher
- 1. The crushing cavity is deep and has no dead zone, which improves the feeding capacity and output.
- 2. Its crushing ratio is large and the product particle size is uniform.
- 3. The gasket-type discharge port adjustment device is reliable and convenient, and the adjustment range is large, which increases the flexibility of the equipment.
- 4. The lubrication system is safe and reliable, the parts are easily replaced, and the maintenance workload is small.
- 5. Simple structure, reliable work and low operating cost.
- 6. Equipment energy saving: stand-alone energy saving 15% to 30%, system energy saving more than double.
- 7. The adjustment range of the discharge port is large, which can meet the requirements of different users.
- 8. Low noise and less dust.
Structure and composition of impact crusher
Impact crusher working environment:
The rotor is the "heart" of the crusher, and it is also the part that is strictly accepted by the impact crusher and plays a vital role in the work. That's why CLIRIK developed and produced heavy-duty rotors with robust construction to achieve a higher moment of inertia. High wear-resistant materials and excellent crushing cavities make the crusher perform well.
The impact crusher has an improved adjustment device and is more convenient to operate.
The three-chamber crushing of the impact crusher has extraordinary performance in fine crushing and ultra-fine crushing operations.
The two-chamber crushing of the impact crusher can simplify the technological process during coarse and medium crushing operations.
Working principle
Impact crusher is a crushing machine that uses impact energy to crush materials.
When the material enters the action area of the blow bar, it is broken by the high-speed impact of the blow bar and is thrown to the counterattack device installed above the rotor to be broken again, and then bounces from the counterattack liner back to the action area of the blow bar to be broken again.
This process is repeated until the material is crushed to the required particle size and discharged from the lower part of the machine.
Adjusting the gap between the impact frame and the rotor frame can achieve the purpose of changing the particle size and shape of the material.
The impact crusher adopts a spring safety device behind the impact plate.
When the non-crushed objects enter the crushing cavity, the front and rear impact frames retreat, and the non-crushed objects are discharged from the machine.
Technical parameter
Model | Specifications (mm) | Inlet Size (mm) | Large Feed Size (mm) | Capacity(t/h) | Motor Power(kw) | Weight(t) |
---|---|---|---|---|---|---|
PF-0608 | Φ644×740 | 320×770 | ≤100 | 10-20 | 30 | 4 |
PF-0807 | Φ850×700 | 400×730 | ≤300 | 15-30 | 30-45 | 8.13 |
PF-1007 | Φ1000×700 | 400×730 | ≤300 | 30-70 | 45 | 12 |
PF-1010 | Φ1000×1050 | 400×1080 | ≤350 | 50-90 | 55 | 15 |
PF-1210 | Φ1250×1050 | 320*770 | ≤350 | 70-130 | 110 | 17.7 |
PF-1214 | Φ1250×1400 | 400×1430 | ≤350 | 100-180 | 132 | 22.4 |
PF-1315 | Φ1320×1500 | 860×1520 | ≤500 | 130-250 | 220 | 27 |
PF-1320 | Φ1320×2000 | 860×2030 | ≤500 | 160-350 | 330-375 | 30 |
PF-1520 | Φ1500×2000 | 830×2040 | ≤700 | 300-550 | 400 | 50.6 |
Related Products
Coarse, Fine, Ultrafine Powder Grinding Mills
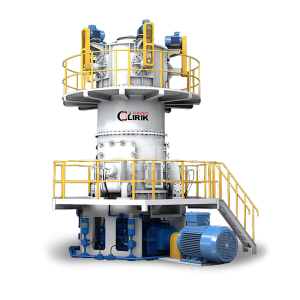
CLUM Ultrafine Powder Vertical Roller Mill
CLUM ultra-fine powder vertical roller mill is mainly suitable for the deep processing of ultra-fine and large-scale powder of non-metallic minerals such as calcite, marble, limestone, talc, barite, brucite, quicklime, gypsum, slag, phosphate, etc.
Capacity: 0.5-45t/h
Finished fineness: 200-3000 mesh
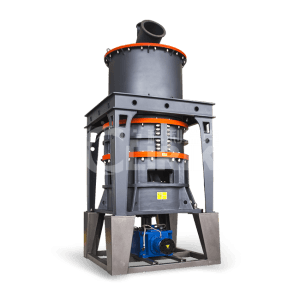
HGM Ultrafine Powder Grinding Mill
HGM Ultrafine Powder Grinding Mill also called ultrafine pulverizer, micro powder grinding mill, limestone grinding mill, calcium carbonate grinding mill. HGM ultrafine powder grinding mill is mainly suitable for superfine powder processing.
Capacity: 0.5-45t/h
Finished fineness: 100-3000 mesh
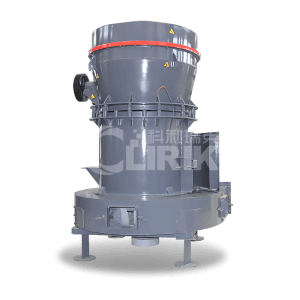
YGM Raymond Roller Grinding Mill
YGM Raymond roller grinding mill is mainly suitable for grinding and processing metallurgy, building materials, chemical industry, mining, and other mineral products.
Capacity: 1.5-40t/h
Finished fineness: 80-600 mesh