Limestone-gypsum Desulfurization Process in Cement Plant
This article takes a 5000t/d clinker cement production line as an example to introduce the design scheme of limestone-gypsum desulfurization.
CLIRIK believe that limestone-gypsum desulfurization technology is very suitable for cement plants.
-
1. The desulfurization efficiency is high (up to 95%).
-
2. Limestone is used as the desulfurizer, and kiln dust can also be used.
-
3. The by-product desulfurized gypsum can be used as a cement retarder.
Reasonable and optimized introduction of limestone-gypsum wet desulfurization technology to the cement industry, compared with the wet desulfurization of power plants with the same waste gas treatment, the investment is reduced by more than 30% and energy saving.
1. Limestone slurry preparation system
Limestone powder (kiln dust) smaller than 45μm is sent to the limestone powder silo, and the limestone powder is discharged into the limestone slurry tank by the impeller feeder, and the process water is added to prepare 30% limestone slurry, and finally the limestone slurry is pumped to absorb Tower circulation pump inlet. The limestone powder of this scheme adopts the ash return of the waste heat boiler of the cement kiln tail.
The complete set of limestone slurry preparation system includes:
(1) Ash back conveyor.
The ash return of the waste heat boiler is transported to the limestone powder bin with a hoist, and the ash collection point is set at the ash discharge conveyor of the waste heat boiler.
(2) Limestone powder warehouse.
The limestone powder silo body is made of carbon steel, and its volume is 40m3, which meets the requirement of 1d. A stand-alone dust collector is installed on the top of the powder silo, and the discharge concentration of the dust collector is less than 30mg/Nm3. The powder bin is equipped with a level gauge, and the discharge port is equipped with a spiral gate.
(3) Impeller feeder.
The impeller feeder is used to transport limestone powder to the limestone slurry tank. The impeller feeder adopts frequency conversion speed regulation, and the feeding amount can be adjusted as required to meet the pulping requirements.
(4) Limestone slurry supply system.
The volume of the limestone slurry tank meets the 2h absorbent consumption of the kiln tail flue gas desulfurization system, and the volume is 8m3. The limestone slurry tank includes a tank body and anti-corrosion, an agitator and necessary connecting pipes, feed and discharge, overflow and drain pipes, level control, inspection holes and all other necessary facilities, flanges, etc.
The limestone slurry pump is used to send the absorbent in the limestone slurry tank to the inlet of the circulation pump of the absorption tower. There are 2 limestone slurry pumps, one for use and one for preparation.
2. Flue gas system
The flue gas from the exhaust fan of the kiln tail is led to the FGD system by the air duct. After the flue gas passes through the desulfurization flue gas baffle, it enters the absorption tower and contacts the spray slurry in countercurrent. The SO2 in the flue gas is absorbed by the limestone slurry, and the flue gas temperature is reduced to a saturation temperature of 53°C. After the desulfurized flue gas is removed by the mist eliminator, the mist is discharged from the wind pipe to the atmosphere through the original chimney.
In order to separate the FGD system from the flue gas of the kiln tail, a total of 2 flue gas damper doors are installed in the flue gas system, including 1 desulfurization flue gas damper and 1 bypass damper. When the desulfurization system is operating normally, the bypass baffle is closed, the desulfurization flue gas baffle is opened, and the flue gas enters the absorption tower through the desulfurization flue gas baffle for desulfurization reaction. In an emergency state that requires the FGD system to be shut down, the bypass damper is automatically and quickly opened, and the desulfurization flue gas damper is automatically closed.
An expansion joint is installed at the entrance and exit of the desulfurization tower to compensate for the displacement caused by the thermal expansion of the flue or wind load. The exhaust gas exhaust fan needs to be pressurized. As the resistance of the desulfurization system is less than 1100Pa, considering the 20% reserve factor, the current exhaust gas exhaust fan needs to be pressurized by 1320Pa.
3. Absorption and oxidation system
The absorption oxidation system is the core of the limestone-gypsum desulfurization system, which mainly includes absorption tower, spray system, demister, slurry circulation pump, absorption tower agitator, flushing system and oxidation aeration system.
The slurry is sent from the liquid storage section at the bottom of the absorption tower to the upper part of the absorption tower through a slurry circulating pump for spraying, and chemically reacts with the flue gas in countercurrent contact, absorbing SO2 in the flue gas, and the CaSO3 produced by the reaction is oxidized in the circulating slurry pool at the bottom of the absorption tower The oxidizing air blown by the fan is strongly oxidized, and fully reacts under the action of the agitator of the absorption tower, and at the same time prevents the deposition in the tower, and finally generates gypsum. The gypsum slurry is discharged by the gypsum discharge pump and sent to the by-product processing system.
After desulfurization, the flue gas is removed by the mist eliminator to remove the carrying water droplets. The two-stage mist eliminator is arranged on the top of the absorption tower in a roof type, and the two-stage mist eliminator is flushed with process water. The flushing process is automatically completed by program control.
The absorption tower adopts a steel tower body and is lined with anti-corrosion materials. Platforms and escalators for maintenance are set outside the absorption tower. The absorption tower is equipped with three spray layers, each spray layer is composed of main pipe, branch pipe, nozzle, etc., so that the slurry evenly covers the cross section of the absorption tower.
There are 3 slurry circulation pumps on the 3 spraying layer. The number of slurry circulating pumps in operation can be determined according to the SO2 change in the exhaust gas of the cement kiln and the requirements for the amount of absorbing slurry. The theoretical design is: when the SO2 concentration at the inlet of the absorption tower is 1200mg/Nm3, all three spray layers will operate; When the SO2 concentration at the inlet of the absorption tower is less than 800mg/Nm3, one spray layer can be shut down to effectively reduce operating power consumption and improve operating economy.
4. By-product processing system
The by-product processing system includes two stages, the first stage is a cyclone, and the second stage is a vacuum belt filter.
The gypsum slurry discharged from the absorption tower is pumped into the cyclone for concentration. The concentrated gypsum slurry enters the gypsum (water content less than 15%) obtained after dehydration by the vacuum belt filter, and is discharged into the gypsum inventory for transportation. The filtrate of the vacuum belt filter and the overflow of the cyclone are all returned to the system for recycling.
5. Process water system
The process water system is mainly used for making up water for the pulping system, spraying in front of the tower, cooling oxidized air, flushing the mist eliminator, water for vacuum pumps, and cooling water for equipment, etc.
The water source of the process water system is the process water in the plant, and the system is equipped with a process water tank and a process water pump. 1 defogger flushing water pump, no spare pump is used.
The flushing water of the equipment, pipelines and tanks and the cooling water of the equipment are recycled to the water collection container or slurry tank for reuse.
6. Accident discharge system
The accident discharge system is mainly used to collect the slurry discharged from the absorption tower during the accident, and return to the absorption tower during operation of the equipment flushing water, pipeline flushing water, absorption tower area flushing water and other area flushing water.
The desulfurization absorption tower is equipped with an accident slurry pool. The accident slurry tank is used to store the slurry in the slurry tank of the absorption tower during the outage of the absorption tower for maintenance. The accident slurry pool is equipped with 2 agitators and 1 accident slurry pool return pump.
A drainage pit is set up in the absorption tower area to collect the tanks, pipelines and drain the slurry and the filtrate of the belt dehydrator. The drainage pit is equipped with an agitator and a drainage pit pump.
7. Compressed air system
The compressed air system utilizes the existing air compressor station in the factory.
It is mainly used for air bag correction of vacuum belt dehydrator and purging of transmitter.
Through the above design, the infrequently used electric valves are changed to manual valves; the filtrate tank and the filtrate flushing pump are abolished and shared with the pit system; the oxidation fan, the demister flushing pump, and the process water pump are not used as backup; the DCS control is changed to PLC Control; the desulfurization tower adopts computer simulation design, reasonable selection of the spray distance from the air inlet to the first layer, improves the desulfurization effect under the same liquid-gas ratio, reduces the circulation pump flow rate and the operating power consumption; adopts flexible configuration of the number of spray layers , To adapt to different SO2 inlet concentrations. It is the better design scheme for limestone-gypsum desulfurization at present.
FAQ
Who we are?
Shanghai CLIRIK Machinery Co.,Ltd. has been committed to the field of ultra-fine powder grinding machines for 20 years.
CLIRIK has a first-class manufacturing base with standardized and intelligent production lines.
CLIRIK's professional R&D, sales, installation and after-sales teams have provided door-to-door services to more than 100 countries and regions.
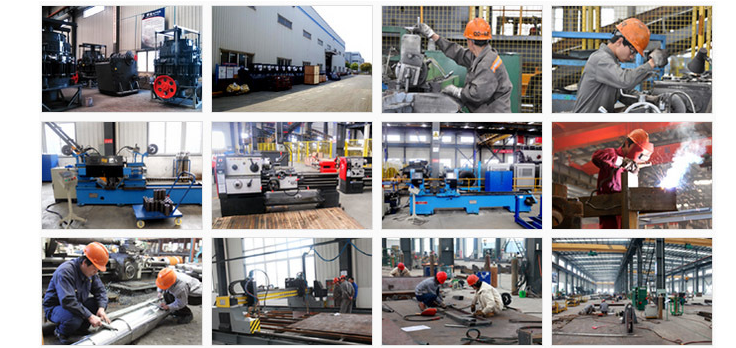
Which models can be selected for processing limestone powder?
How to get the latest quotation?
You can leave a message online or contact CLIRIK directly:
Email: sales@clirik.com
WhatsApp: +8613512155195/+8613917147829