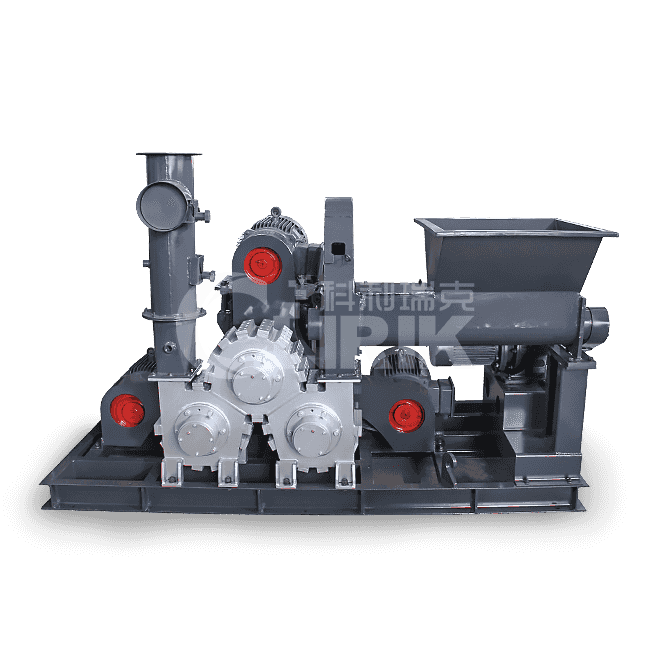
Stone Powder Surface Coating Machine
Stone Powder Surface Coating Machine is also named the powder surface modifier.
It is an inevitable product of the development of modern high technology and new materials.
Powder surface coating machine is widely used in non-metallic mineral fillers or pigments such as plastics, rubber, binders, and other modern polymer materials, high Material-based composite materials, functional materials, and coatings industries.
Features Of Powder Surface Coating Machine
Stone Powder Surface Coating Machine is an inevitable product of the development of modern high technology and new materials.
It is widely used in non-metallic mineral fillers or pigments such as plastics, rubbers, binders, and other modern polymer materials, polymer-based composite materials, functional materials, and coatings.
In other industries, after the mineral powder is modified, it can not only greatly improve the compatibility of inorganic mineral fillers and organic polymers, improve the interfacial bonding force, enhance the mechanical strength and comprehensive performance of the material, but also greatly improve the powder.
The filling amount of the bulk filler can reduce the production cost, and at the same time, it can endow the product with some special physical and chemical properties.
However, the interface properties of most common non-metallic mineral materials and organic polymer matrix are different, and the compatibility is poor, and direct or large filling will lead to the decline of some mechanical properties of the material. Therefore, surface modification of inorganic mineral fillers is very important.
The unique modification chamber design of the modification machine has both modification and depolymerization functions, and is suitable for modification of various materials, such as counterweight, light calcium carbonate, various kaolin, talc, wollastonite, quartz powder, mica , silica, titanium dioxide, zinc oxide, alumina, magnesium hydroxide, barium sulfate, illite, pyrophyllite, tremolite, etc., all have good surface modification effect.
Modifier Performance Advantage
The performance characteristics of the modifier
- 1. The unit can run continuously for production and has a large processing capacity, which is suitable for industrial production of various scales.
- 2. The use rate of the modified agent is high, the dosage is small, the powder coating rate and activation index are high, and the energy consumption is low.
- 3. The equipment has both modification and dispersing functions, and is suitable for materials of various fineness. It has a unique modification and activation effect on materials with small false specific gravity and large bulk density ratio, such as white carbon black, mica powder, talcum powder, etc.
- 4. The high-speed gas-solid vortex mixing operation of the powder and the agent has high modification efficiency and basically does not destroy the original particle shape of the powder.
- 5. The material is operated under negative pressure, with good sealing performance, no dust leakage, basically no pollution, good operating environment and low labor intensity.
- 6. The heating and cooling are completed in one machine, no separate heating and cooling systems are required, and the operation is simplified.
- 7. Independent fluid and non-fluid dosing system, continuous, stable and uniform.
Structure And Composition Of Modifier
The structure of the modifier
1. Hopper: The material enters the hopper directly from the hopper, and the moisture content of the material should be less than 0.5%.
2. Feeding device: It adopts twin-screw feeding, and the speed is adjustable, which can ensure the stability of material flow.
3. Temperature control dosing system: automatic temperature control, the melting temperature of the drug can be set arbitrarily, suitable for various modified drugs in the form of solid and liquid.
4. Modification host: The modification host is composed of three character-shaped modification cylinders, with compact structure, high modification efficiency, and stable and reliable operation.
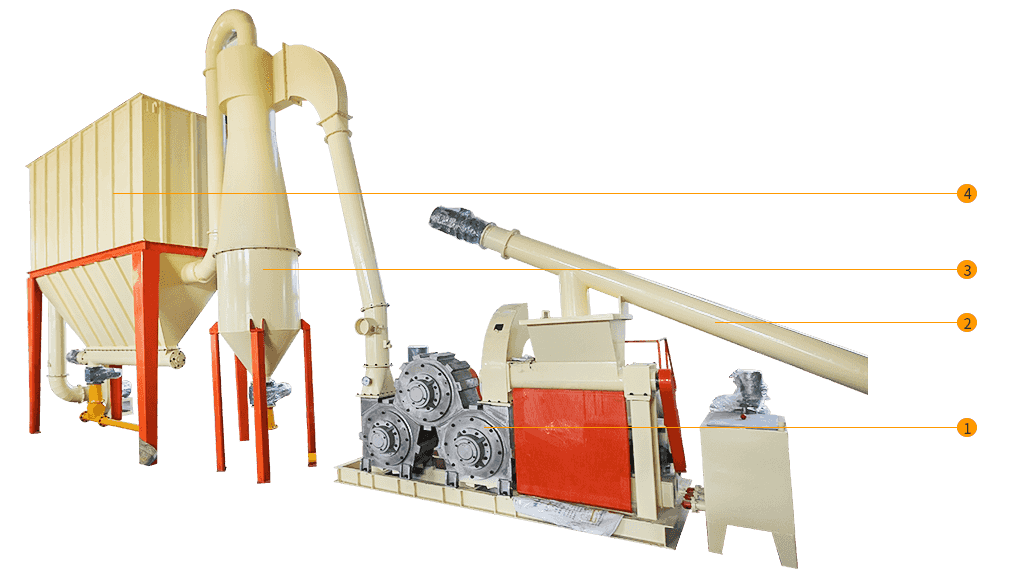
1 Modifier 2 Screw conveyor 3 Powder collector 4 Dust collector
Matters Needing Attention In The Work Of The Modifier
1. The influence of impurities, the impurities of non-metallic powder are mainly the original impurities of the raw materials and the impurities generated during the processing. When controlling the impurities of the raw materials, the pollution of the processing equipment and the problem of impurity removal should also be considered.
2. Selection of surface modifier of modifier machine. In the surface modification of non-metallic powder, the selection of surface modifiers is very important.
Modifier Working Principle
The working principle of the modifier
The powder raw material is sent to the atomization chamber above the main machine through the feeding conveying system. During the conveying process, the powder is heated and dried by the special heating device of the feeding conveyor. At the same time, the solid modifier is used in a special The inside of the heating container is also heated and melted to a liquid state and then sent to the atomization chamber through the conveying pipeline.
There are two groups of nozzles in the atomizing chamber, one of which has four nozzles distributed on the inner wall of the atomizing chamber according to different positions, and its function is to blow the powder material sent by the conveying system into a mist. At this time, the raw material and the reformer form a mist. Due to the effect of two sets of nozzles spraying air from different directions, they can be fully mixed, that is, enter the host.
The main machine is composed of a high-speed rotating main shaft, a stirring rod, an impact hammer, etc. The atomized material entering the main machine is subjected to impact, friction, shearing and other effects under the high-speed stirring of the stirring rod, so that the powder particles and modifier can be obtained. After full contact and mixing, the powder material has been fully coated and modified.
The modified material is sent to the finished product collection bin by the screw conveyor. During the air conveying process, the excessive heat in the material is absorbed by the conveying air flow, and is discharged to the outside after being dedusted by the bag filter. The finished product can enter the collection bin. to a storable temperature.
Powder Surface Coating Machine Technical Parameter
Model | Main Motor Power(KW) | Powder Machine Power(KW) | Spindle Speed | Yield(t/h) | Weight(t) | Dimensions(mm) |
---|---|---|---|---|---|---|
CLG-200D | 3*4 | 2.2 | 5700 | 40-150 | 1 | 3200*600*2200 |
CLG-3/300D | 3*18.5 | 5.5 | 4500 | 500-1800 | 3 | 5800*1800*5600 |
CLG-3/600D | 3*37 | 15-22 | 2700 | 2000-4000 | 10 | 11200*3100*6200 |
CLG-3/900D | 3*75 | 45 | 2000 | 4000-7000 | 20 | 21000*3800*6500 |
Related Products
Coarse, Fine, Ultrafine Powder Grinding Mills
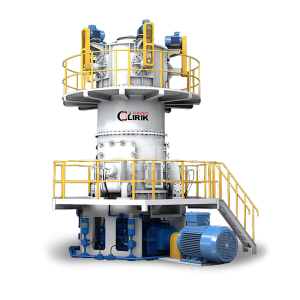
CLUM Ultrafine Powder Vertical Roller Mill
CLUM ultra-fine powder vertical roller mill is mainly suitable for the deep processing of ultra-fine and large-scale powder of non-metallic minerals such as calcite, marble, limestone, talc, barite, brucite, quicklime, gypsum, slag, phosphate, etc.
Capacity: 0.5-45t/h
Finished fineness: 200-3000 mesh
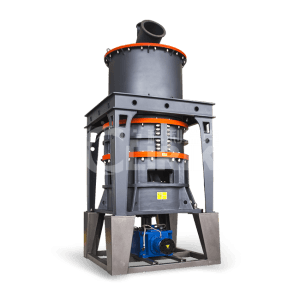
HGM Ultrafine Powder Grinding Mill
HGM Ultrafine Powder Grinding Mill also called ultrafine pulverizer, micro powder grinding mill, limestone grinding mill, calcium carbonate grinding mill. HGM ultrafine powder grinding mill is mainly suitable for superfine powder processing.
Capacity: 0.5-45t/h
Finished fineness: 100-3000 mesh
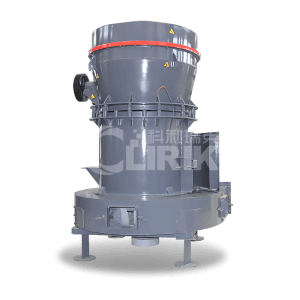
YGM Raymond Roller Grinding Mill
YGM Raymond roller grinding mill is mainly suitable for grinding and processing metallurgy, building materials, chemical industry, mining, and other mineral products.
Capacity: 1.5-40t/h
Finished fineness: 80-600 mesh